Things You Should Know About Steel Silo Project Construction
There are many things you should care about when building a steel silo. The following are the detailed things you should keep in mind.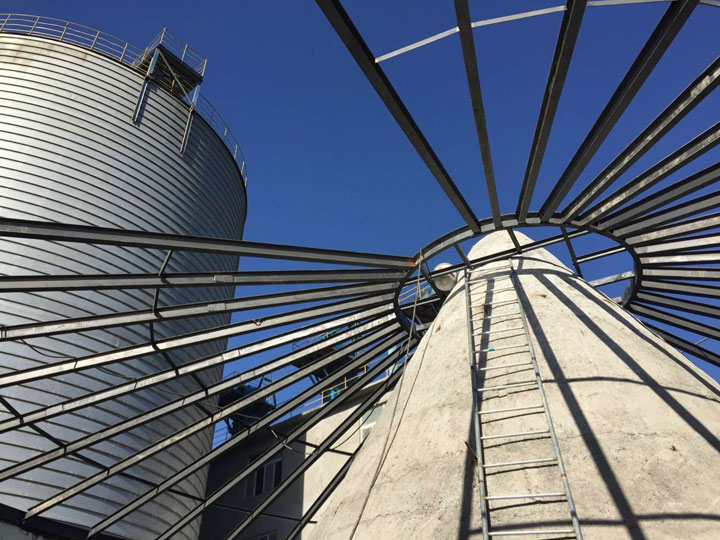
Foundation Acceptance
- To check the construction of the steel silo in this project of construction foundation embedded component distribution, layout of the size, location, quantity according to the technical requirements and design drawings,.
- To confirm the stability, carrying capacity and the basic level of the temporary construction platform.
- Basic conditions should meet the requirements, the construction of steel silo base platform delivery.
Plan the Root Installation Line of Steel Silo
- After the construction of the steel silo is delivered, according to the diameter and position specified in the design drawing, plan the root installation line of steel silo.
- Clean the construction site, completes the preparation work before construction.
Construction Materials, Equipment, Components Enter and Inspection
- According to the enter inform, sent the construction of the engineering equipment, fittings, engineering prefabricated components, auxiliary materials to the site.
- Prepare and arrange engineering construction equipment and tooling, engineering prefabricated component, project profile, coil and auxiliary materials subsidiary details and proof materials inspection, submitted to the project supervision department inspection, review and approval.
- According to the requirements of supervision engineers, use the main materials of project to produce test samples, report the inspection result to the supervision department of the project for review and approval.
Construction Materials, Equipment, Components Lifting Platform
After receiving the notice of approval of the Ministry of supervision of the project, put the construction equipment, the engineering engineering engineering fittings, prefabricated components, main and auxiliary materials transported to the site on the lifting platform.Layout and Stacking of Construction Materials, Equipment, Components
- According to the provisions of the " Lipp steel silo construction equipment operation manual", bending machine should be placed in temporary construction equipment platform at one end of the bending machine export direction, forming machine placed in the direction of the tail of the bending machine, decoiling machine placed in the direction of the tail of the forming machine.
- Construction coil material according to the thin thickness after placed before decoiling machine the location of the pair in the back.
- Stiffener placing method, put the first used on the top, after used on the next, mall model material on the top, big model material on the next.
- Steel silo roof material, component placing method, put the first used on the top, after used on the next.
Arrangement, Installation and Adjust the Construction Equipment and Column Frame
- Mark down position line to determine the position of the frame of the construction equipment, find the basic platform level.
- According to the " Lipp steel silo construction equipment operation manual" arrangement and installation of equipment in place, adjusting equipment’s silo radial horizontal and Circumferential lift angle.
- According to the " Lipp steel silo construction equipment operation manual" arrangement and installation bearing support, connection frame, adjust the bearing support arm angle, guide wheel helix angle.
- And put the material cloth in the designated spot.
Debugger Construction Equipment, Trial Run and Construction Preparation
- Turn on electricity, debugging and linkage trial run.
- Adjust the running clearance of forming machine and bending machine parts.
Steel Slo Construction
- In accordance with the steel silo design drawings provisions of the specifications of the coil, use triangle bracket and triangle bracket lifting on the decoiling machine.
- Cutting bending plate head into a cone shape, let it enter the forming machine, feeding and start rolling.
Silo Wall Closure
- When coil is processed into the groove on the combination of coils on upper and lower rings by forming machine, according to lipp steel silo construction equipment operation manual, the size of its shaped notches of grooves shall be checked. And after that, eligible shaped coil is put into entry guide of bar folder and further its notch is made into the sectional shape of flat round convex strip by rolling. (Here exists the slant upward 45° angle between long axis direction of sectional flat round convex strip and surface of steel silo body, which has formed continuous annular convex rib which can strengthen annular load capacity. ) The coil processed by bending machine to be in completion status moves forward a circle along supporting guiding wheel of column arm and close together with shaped coil on the lower ring before bending machine.
- Before closure of coils of steel silo wall, measure whether the length of shaped coil is in accordance with specification of design or not, grooves on combination of eligible shaped coils on upper and lower rings coincide with each other. Upper groove of shaped coil on lower ring snaps into the inside of lower groove of shaped coil on upper ring. Mutual biting grooves are sent into bending machine to complete biting connection and accomplish closure of coil walls.
- The steel silo wall coil closure through the bending machine and then continue to move 1 to 2 meters, use the vernier caliper check the thickness of the spiral bite. Adjust bending machine outlet edge thickness conform to the "Enterprise standard" (That is: 5d∠D≤6d. d for coil thickness, D for article convex thickness), then start rolled the steel silo.
- Normal rolling the silo body and install the steel silo wall horizontal cutting machine cutting head horizontal lines
- Continue rolling while two to three times volume then parking, installation the steel silo roof.
Install the Steel Silo Down Tension Ring
- After cleaning, regular wall head horizontal cutting line, reported to the supervising engineer's interim review of steel silo wall plate thickness specification and the upper diameter of the steel tube (use a steel tape measure perimeter calculate the diameter of the cylinder).
- Used after confirmed J422Φ3.2mm electrode, choose 200A-260A current, welding processed down tension ring to steel silo upper provisions parts.
- Adjustment the silo body upper oval to conform to "the provisions of the standard" deviation of range (using a steel tape measure to measure the diameter of the silo body, the difference between the maximum and minimum diameter, ellipse deviation of steel silo)
- Divide the purling bottom line installation
Installation the Upper Tension Ring and Purline
- Upper the upper tension ring divide the assembly line upper purling line, use support frame set up upper tension ring, adjust the mounting direction of the upper tension ring, make the assembly line coincide with the silo barrel radius ray (using horizontal stay and vertical line to determine).
- Determine the spring height of silo roof (use the steel rule measuring the vertical distance from the bottom of upper tension ring to horizontal stay).
- Use J422 Φ4.0mm electrode, choose 260A-340A current, welding purline and upper tension ring, down tension ring, welding the two ring to brace between the purline. installed steel silo roof keel frame, submitted supervising engineer occasional survey the quality of keel frame soldering seam. Installed cover plate after qualified (upper covering).
- When installing silo roof keel frame, the operator who stand on the keel frame should ware safety belt, add the temporary hanging safety belt ring on the upper tension ring, ensure the safety of the high altitude construction operator.
Install Top Cover
- Use the lap welding or landfill welding way to install top cover(upper covering)
- Lap welding is put an edge of cover plate intermittent welded together with the purling line, the edge of another cover plate up on previous cover plat, lap seam welding. There shall be no slag, porosity, fissures and cracks in the welding seam, and the thickness of the weld is greater than the thickness of the welded plate.
- Landfill welding is put each one side of two cover plate on the purling line, the distance is 4mm, welded two cover plate and purline together at the same time. There shall be no slag, porosity, fissures and cracks in the welding seam, and the thickness of the weld is greater than the thickness of the welded plate.
- Use J422Φ3.2mm electrode install cover plate, choose 260A-320A current,after welding, to clean up the weld and the fusion splash, submitted supervising engineer occasional survey the quality of cover plate weld seam.
- When install top cove, due to the large slope of the top, the operator stand on the cove, should wear anti-skid safety shoes, prevent the accident from sliding off the cove. When necessary, the operator should wear a safety belt, and the safety belt is hung on the reliable hanging sleeve.
Silo Roof Inner and Outer Surface Coating
After steel silo cover plate is welded and complete the inspection, to clean up the weld and the fusion splash, clean up the burnt rust primer welding component.On weld and both sides paint rust-inhibiting primer, in accordance with the provisions paint next rust-inhibiting primer and surface paint.
Install Guardrail Vertical Pole
- After cover plate is welded, in the lower stiffener and down tension ring binding site full weld top vertical bar, one side of the plane of the pole angle inward, stud side outwards.
- Let round shaped handrails and pole welded into one.
- Measurements divided into flat iron fence installation line, welding guardrail flat iron and pole spot into one, the overlap of guardrail flat iron is full welding the two side seam.
- After guardrail welding quality is qualified to clean up the welding seam, in accordance with the provisions paint the fence paint, steel structure roof production and installation of all completed.
- Use J422Φ3.2mm electrode install guardrail, vertical pole, choose 200A-260A current.
- Install guardrail, vertical pole, if there is no safe operating position and situation, the operator should wear a safety belt, and rope sleeve the safety belt, temporary hung on an guardrail vertical pole which is welded well or handrails.
Roll Silo and Stiffener Installation
After the cover plate installation is complete, according to the design requirements and installation quantity dividing stiffener mounting line, rolling the steel silo, rolling the silo wall to a certain height, as the varieties, specifications, sizes stipulated in the design drawings, welding stiffeners (inside the silo).In delimited stiffener installation line, use spirit level determine stiffener squareness, the upper of stiffener withstand the bottom of cover plate down tension ring, spot welding with the wall, then the stiffener is welded together with the exposed joint of the down tension ring
- Up and down and left and right sides of the seaming of stiffener and silo wall, the welding length is greater than or equal to 50mm, and the thickness of the weld is greater than the thickness of the welded plate.
- The two section of the stiffener is connected with the connecting plate according to the design drawing specification,connecting plate with two stiffener exposed seams using such strong seam full welding connection, and the thickness of the weld is greater than the thickness of the welded plate.
- Connection and assembly of stiffener, generally use such strong welding, to meet the demands, the groove bottom seam requires increased clearance or breach, ensure the quality of the welding seam is in conformity with the specification.
Outside Surface Welding Point Brushing Paint
- Clear the out side welding point oxide skin, paint all the paint required by design drawing (after the first paint dry then brush next paint.
- The exchange of silo coil
- During the coiling of silo, one coil winding is completed and replace the next coil,use corner ruler or T-square mark cutting line, and use the portable grinding wheel cutting machine removed Irregular plate roll.
- For one coil roll completed, put the well trimmed coil joint control in the entrance of forming machine of around 500 mm.
- Take the next volume coil, using triangle bracket and electric reverse chain hoisting to the decoiling machine machine, pull out the coil end socket.
- Using the same method removed and trimmed the next coil end socket, welding two pieces together, use J422Φ2.5mmelectrode, choose 200A-260A current, from both sides top-down to welding.
- Coil butt weld welding, the welding line shall be flat and interratic, forbidden slags, pores, cracks, and the thickness of the weld is greater than the thickness of the welded plate.
- Outer surface of welding seam shall be painted in accordance with the regulations.
Replace Different Specifications of Coil and Stiffener
- During the coiling of silo, all height according to the design drawing, when replacing coil with different specifications, must submitted supervising engineer for temporary inspection and examination, and fill in the inspection sheet of concealed steel silo project, after the confirmation can continue to manufacture and install steel silo.
- The replace of different specifications of coil is same as clause 4.5.17.
- Replace different specifications of stiffener, submitted supervising engineer occasional survey the quality of keel frame soldering seam, must submitted supervising engineer for temporary inspection and examination, and fill in the inspection sheet of concealed steel silo project, after the confirmation can continue to manufacture and install steel silo.
Continue Roll the Silo to Specified Height, Cutting Horizontal Line of Lower Opening of Silo
Silo Landing
- After the silo landing, use the odolite to observethe perpendicularity and ovality of silo, if the deviation is more than the"enterprise standard" provisions, by adjusting the height and angle of the support arm of upright post, adjust the perpendicularity and ovality of silo, when conform to the standards, submitted supervising engineer for review confirmation.
- After the perpendicularity and ovality of silo meet the standards, welding and installation silo wall stiffener to the steel silo foundation embedded component. The relative position of foundation embedded component and root stiffener, deviation exceeds the drawing requirement for 75mm. Should issue the remedial measures or program by the relevant technical departments, and in strict accordance with the corrective actions or plan construction.
- For the relative position of foundation embedded component and root stiffener, deviation exceeds the drawing requirement for 30mm-75mm, increase the stiffener between foundation embedded component and root stiffener for remedy.
- The connection of foundation embedded component and root stiffener, must be in accordance with the requirements of design drawings, full weld the exposed welding seam, and the thickness of the weld should meet the requirements of construction design drawings.
- After completed the welding of all the steel silo root stiffener and foundation embedded component, the manufacture and installation of steel silo is all over.
Installation of Steel Silo Auxiliary Hole, Port
- Silo door installation: after silo landing, according to the location, height, opening size and installation requirements of the design drawing, mark the edge of the hole line, oxyacetylene cutting door installing hole, mark the position of bolt hole. Drill, inner and outer door flange, bolt fastening, and paint.
- Withdrawal, removal of equipment support, transfer site or location
- During the coiling of silo, according to provisions of the "enterprise standard" of inspection items and frequency, to test the various parts of the steel silo, and timely record in detail the test data in engineering construction quality of steel silo in the inspection report, timely and in accordance with the regulations report engineering project supervision department supervision engineer for review.
Get In Touch With