steel silo development
From riveted silo, welded silo, assemblage silo to spiral silo, the development of steel silo has a history of more than 100 years. Originated from the early 20th century, steel silo has been widely applied in western countries and almost replaced all the other types of silos in grain storage industry in the late 1970s. At present, 95% of grain silos used in the United States is steel silos.
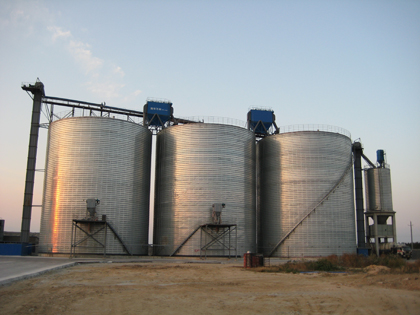
Steel silo technology in grain storage industry started late in China. In 1982, an assemblage silo group constructed with galvanized corrugated sheet has been imported from the United States to Honghe Farm in Heilongjiang province. It is the earliest modern steel silo group in China. In the 1990s, Chinese steel silo industry achieved unprecedented development. Entering the 21st century, Jiangsu Zhengchang Group imported a complete set of technology of assemblage silo and professional production line from the United States. On the basis of assimilating the most advanced technology, design software, manufacture standards from western countries, Zhengchang Group implemented innovation and development to produce, manufacture and install assemble silo massively with better performance on strength, capability and security. Zhengchang Group, who first exported steel silo as a product of China, is now the representative of China’s international level on production, manufacture, and installation in steel silo industry, as well as the navigator of the entire steel silo industry around the world.
Now the steel silo is extensively applied in the storage of granule, powder, grain, oil, brewage, coal and building material etc, as well as in the areas of industry, agriculture and environmental protection.
The First Generation of Steel Silo
First generation steel silo is a physical structure designed according to “National Design Specification for steel Concrete Silo GBJ77-85”. The wall of the silo is made of cement concrete or riveted steel. The first generation steel silo is a product of rapid development of industry in the late 20th, which is not suitable for promotion because of some technical problems. The major representatives are enterprises such as local industries, cement design institutes, cement plants, and ready-mixed concrete companies etc. Because of its small volume, the first generation steel silo generally has a capacity of hundreds or thousands of tons.
The Second Generation Steel Silo
The second generation steel silo is also known as assemblage steel silo. Its technical features are as follows: 1. Manufactured with hot galvanized steel, the assembly steel silo is composed with national standard parts whose replaceability can extend the silo’s service life. 2. The assemblage steel silo is transformable and relocatable, making it ideal for customers who rent spaces. 3. The dimension of the assembly silo could be customized within a comparably large range. Compared with traditional concrete silo, the assemblage silo has been greatly improved in structural design and application. However, it still inherits traditional techniques on mechanical structure and electrical controlling system. Unavoidably, there are technical defects such as the lack of intelligent control on loading, unloading and storing materials, backward technology and too much manual intervention. Therefore, it is hard to monitor the status of storage and preserve materials without deterioration over a long term.
The Third Generation Steel Silo
The third generation steel silo is also known as spiral steel silo. Its technical features are as follows:
Advanced Technology: Spiral silo is constructed with special equipment when it was built. In the process of rolling, the ektexine of the silo was made to a spiral convex band with thickness five times more than the material, and width of 30 to 40 mm, which highly strengthened the carrying capacity of the silo, and make the overall intensity, stability as well as shock resistance preceding over other silos.
Good Sealing Performance, Wide Application: By use of special equipment for bending and seaming, and ensuring the quality of all parts of the silo body in process, the seal of the silo is particularly good. Therefore, by using the silo for storage of granule, powder, grain and alike, as well as storing liquid material, the process requirement of pesticides and fumigation can be well met.
Comparably Short construction period, Competitive price and small coverage: Short duration can be guaranteed for our professional equipment can provide a 5m per minuets’ shaping and bending speed and no auxiliary facilities like scaffolding are needed during the whole procedure. The weight of spiral steel silo is just as heavy as 1 / 6 of the concrete silo, so that the cost for the entire project can be largely reduced. Comparably small coverage that could narrow the separation distance down to 500mm for maximized space utilization.
Get In Touch With