How to Protect Chemical Tank from Corrosion
Chemical storage tanks are mainly used for storing chemicals. Different from grain bins and cement silos, chemical properties of chemical tank surface must be stable so that it can’t react with chemicals. Chemical containers can be classified into different sizes and shapes, and they can be used to stationary storage, processing, or other purposes. Chemical storage tanks can be store gasoline, diesel, propane, liquefied gas and other dry bulk chemicals. They are usually utilized at industry sites, farms, and gasoline stations.
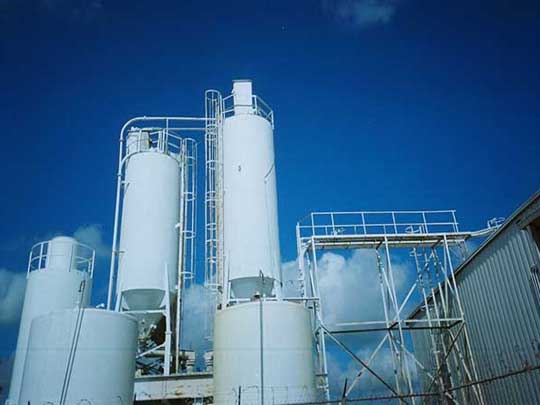
Chemical tanks can be classified into two types: underground chemical tank and above-ground chemicals silo, these two types are widely used in the field of industry.
Underground Chemicals Storage Tank
Underground storage tank is a nice choice for maximizing the property use, because it can be constructed underground, whether under lawns or gasoline stations. Installation under the ground reduces the risk of fire and explosion and prevents the tanks from natural disasters such as hurricanes and tornadoes. But the underground tanks containing petrol or other dangerous chemicals may leak. And it will contaminate the soil and the ground water. This posts the health of local residents and home nearby into great danger. Therefore, it is vital to inspect the tank after the installation.
Above- ground Chemicals Storage Silo
Above-ground chemicals storage tank, also called above-ground chemiclas storage silo, is suitable for storing chemicals and fuels in bulk. It is also widely used owning to the low cost and easy installation. Compared with underground container, it is easily to check for the leaks and carry out the repairs. But the disadvantage is that it may be influenced by the environmental conditions such as fire, whether and explosion.
Coating Technologies of Chemical Storage Tank
There are many kinds of industrial liquid chemicals need to be stored and processed. Each has different properties and may corrode the surface of the containers. Coating technologies is applied to the installation of storage tanks to resist corrosion. Coatings of the tanks provide corrosion and abrasion resistance to the stored chemicals. They can extend useful life and reduce maintenance cost of chemical containers. Coating technologies include epoxy coating, glass fused-to-steel, high heat coatings, cold weather coatings and etc. Galvanized storage silo is also popular, and it is suitable for storing block or dry bulk chemicals.
Epoxy coating is most commonly used in the coating technologies whether for the storage of liquid or dry bulk. When applied in use, epoxy coating comes to a good effect without any trace of breaking and tearing.
Coatings play an important factor in securing the safety of tanks and chemicals. Some coatings are applied to the storage of a large number of products. Before putting into use, the most important thing is ensuring that the coating tank is suitable for the application. Some coatings may react with certain products. In addition, the requirement of liquid storage tank is more stringent than that of dry bulk storage tank.
Before using an old tank to store a new products, remember to test and inspect whether it is suitable for the application. Be sure that the tank can resist the corrosion. Incorrect use of a tank may cause huge losses.
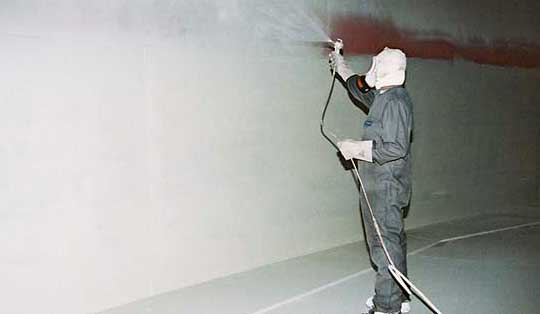
Coating technologies not only protect storage tanks, but also prevent the environment from being polluted. The use of coating is the long term plan for the manufactures and owners. The development of coating technology is the integral parts in the industry of tanks. Corrosion control of chemical containers is vital, and it must corporate related knowledge and the practice. Those professionals must recognize the early signs of corrosion and maintain the tanks immediately to ensure the effective protection of environment and the economic interest.
Both underground chemical storage tank and aboveground chemical storage tank all could leak harmful substance. Which may contaminate our soil and water, pollute the environment and do harm to our health. In one word, corrosion is to blame. We should try our best to engage in the control of corrosion. With the help of coating technology, people can protect the environment and improve the economic interest effectively.