Everything You Need to Know About Silo Materials
The silo is a cylindrical warehouse used for storing bulk materials. It is mainly divided into two categories: agricultural silos and industrial silos. Agricultural silos are used to store grain, feed, and other granular and powdery materials, while industrial silos are used to store coal, cement, petroleum, chemical raw materials, etc. With the progress of the times, equipment that conforms to the trends of mechanization, automation, technological advancement, and large-scale production will surely be rapidly popularized. Mechanized silos are now widely used in the storage processes of both agriculture and industry, serving as indispensable components within their respective fields.
For centuries, silo structures, serving as crucial storage units for various materials such as grain, cement, and chemicals, have evolved into a diverse array of materials. The diversity of materials used in constructing silos reflects the unique storage requirements of different industries and the technological advancements in material science. From traditional materials like wood and concrete to modern alloy steels and composite materials, silo construction has continuously evolved to meet the demands for efficiency, durability, and safety. The following will introduce the classification of several common silo materials and briefly describe their advantages and disadvantages.
Classification of Silo Materials
Wooden Silos
Wooden silos are the earliest form of silo structures in history, commonly found in granaries and farms. Nowadays, some abandoned wooden silo sites have been renovated and repurposed into unique attractions. Constructed from wood, wooden silos are typically cylindrical or polygonal in shape. They offer natural insulation properties, along with advantages such as lightweight, low cost, easy installation, and natural ventilation. They are suitable for storing crops such as rice, wheat, and corn. However, over time, their susceptibility to decay, flammability, vulnerability to pests, and mold growth, among other disadvantages, have led to the development of alternative materials.
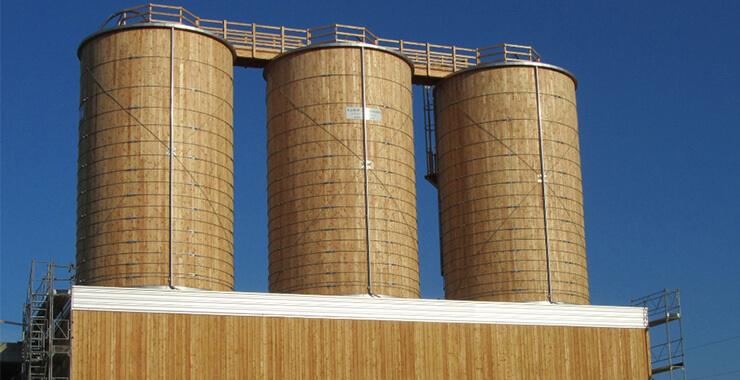
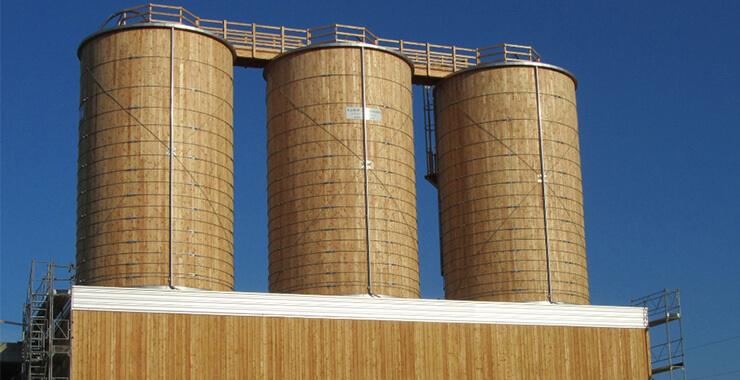
Concrete Silos
Concrete silos are constructed using reinforced steel, cement, and gravel, typically in the form of tall cylindrical or conical structures. They possess excellent overall integrity, capable of being poured as a single unit and reinforced with steel, enabling the long-term safe storage of large quantities of materials. Widely utilized in civil engineering projects, concrete silos exhibit high durability, fire resistance, large storage capacity, long lifespan, resilience to weather and environmental conditions, and low maintenance costs, making them suitable for large-scale industrial applications. However, their drawbacks include high initial construction costs, lengthy construction periods, limited flexibility for modification or expansion, inability to be easily demolished, lower safety control, susceptibility to cracking over time if improperly maintained, difficulty in repair processes as time progresses, etc.
Concrete silos are currently used for storing materials in industries such as cement, mining, agriculture, biofuels, clay, and limestone.
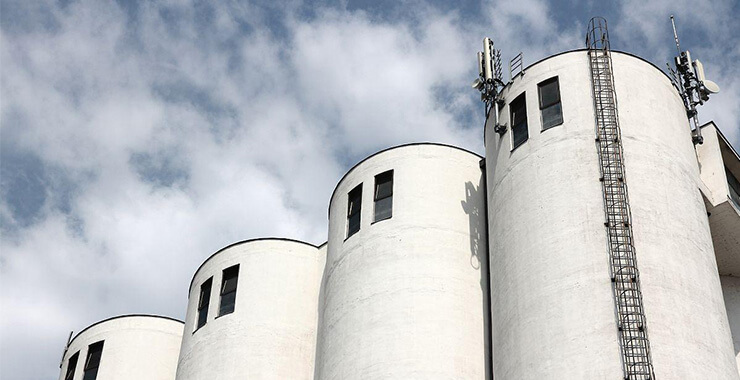
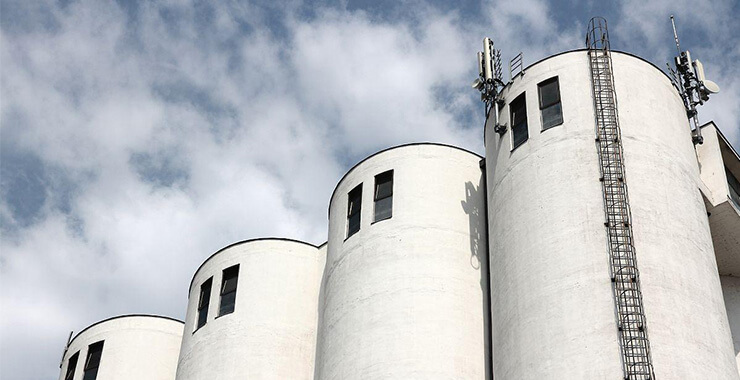
In the industrial field, concrete silos are typically utilized for storing powdered or granular materials such as cement, coal powder, and fly ash. They can also be used for storing petroleum and chemical raw materials. Reinforced concrete silos boast excellent sealing and stability, ensuring materials remain dry, without leakage or clumping.
In the agricultural domain, concrete silos are primarily employed for storing grains, feed, and other agricultural products. Due to the large storage capacity and long service life required for agricultural products, concrete silos are widely used in rural areas.
In civil engineering, reinforced concrete silos serve as structures for residential, commercial, and recreational purposes, including underground parking lots, underground shopping malls, basements, and sports arenas. They can withstand high water pressure and soil pressure, offering good seismic resistance, durability, and insulation, meeting the diverse needs of different buildings.
Steel Silos
With the overarching trend of modern technological advancement, the progress in metallurgical technology has made steel the primary material for silo construction. Steel silos, made from steel plates, are typically cylindrical. These structures boast large volumes, durability, corrosion resistance, and reusability, and are less prone to pollution. They are commonly utilized for storing bulk materials in both agricultural and industrial settings. Additionally, steel silos offered by AGICO can be customized to meet specific requirements, such as ventilation systems for grain storage or temperature control systems for temperature-sensitive materials.
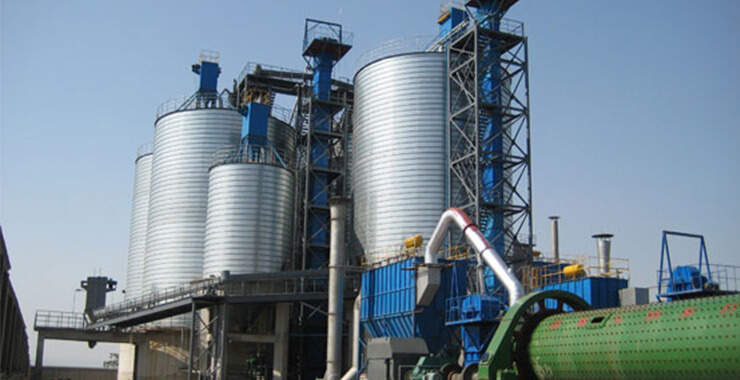
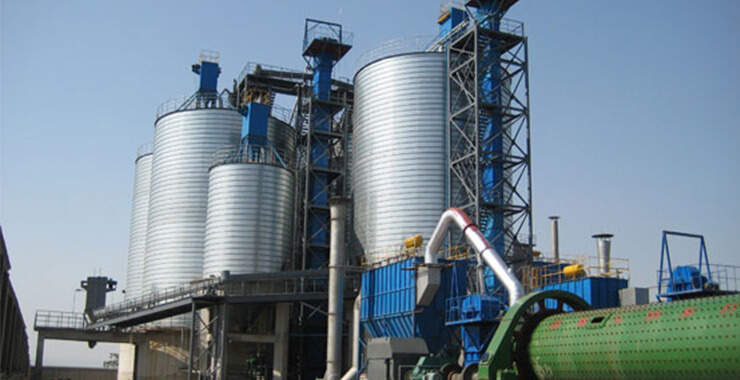
Advantages of steel silos:
1. Superior overall performance and long lifespan: Constructed entirely with specialized equipment, steel plate silos exhibit enhanced load-bearing capacity, structural strength, stability, and seismic resistance compared to other silo types. Furthermore, the selection of optimal plate materials based on the material's corrosive and abrasive resistance requirements ensures a normal service life of 30-40 years, far surpassing other silo types.
2. Excellent airtightness and versatile usage: Utilizing specialized equipment for bending and sealing, steel plate silos ensure quality throughout the entire structure, making them particularly well-sealed. They can store powdered materials such as cement, fly ash, and superfine slag, finding widespread application in the construction materials industry, including cement plants, power plants, and grinding stations.
3. Short construction period and low cost: Our seam welder can shape silos at a rate of 3-5m per minute. A 1000-ton cement silo can be completed in just 5-7 days.
4. High strength: The continuous spiral bite of steel plate silos is five times the thickness of the base material, significantly enhancing their load-bearing capacity.
5. Small footprint and lightweight: AGICO steel silos offer flexibility in height and diameter selection, with a minimum distance of 50 cm between two silos, maximizing space utilization and reducing footprint. The self-weight of steel plate silos is only 1/6 of that of concrete silos of the same volume, significantly reducing foundation loads and construction costs.
6. Furthermore, construction of steel plate silos is largely unaffected by seasonal or weather-related factors, enabling enterprises to quickly achieve significant economic benefits.
For detailed equipment parameters, please refer to the following page. AGICO can customize personalized steel silos for various fields such as:
- Cement Silos
- Lime Silos
- Coal Silos
- Slag Storage Silos
- Calcined Petroleum Coke Storage Silos
- Fly Ash Silos
- Wastewater Storage Tanks
- Chemical Storage Tanks
- Grain Silos
Plastic Silos
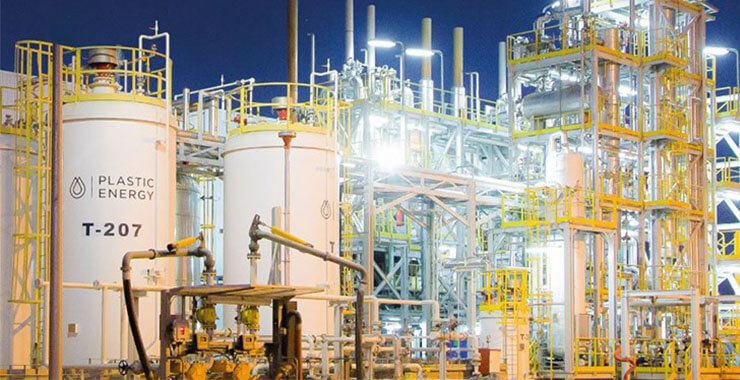
Plastic silos are generally made of polyethylene material, featuring lightweight, flexible capacity, easy installation, easy cleaning, and low transportation and installation costs. This type of silo is suitable for storing materials with relatively small single-bin quantities, such as animal feed, dry salt, grains, lime, plastic pellets, and other dry products. The shape and size can be customized, typically cylindrical, conical, or trapezoidal. Plastic silos have a price advantage compared to other silos, but their drawback lies in their lack of durability. Compared to metal silos, plastic silos are more prone to aging, deformation, cracking, and other issues. Additionally, plastic grain storage bins have relatively low load-bearing capacity, making them less suitable for large-scale material storage and more suitable for use in small-scale factories.
Fiberglass Silos
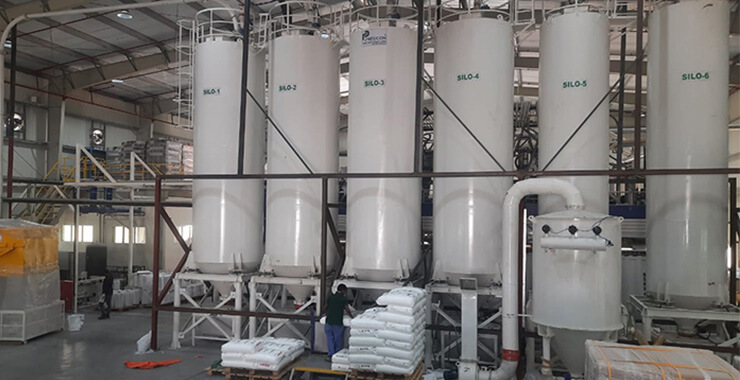
Fiberglass silos are made of materials such as polyester resin and fiberglass. Fiberglass has the advantages of being lightweight, high in strength, non-corrosive, and excellent insulation, making it an ideal material for thermal protection and corrosion resistance in situations of instantaneous high temperatures. Fiberglass silos are suitable for storing salt, feed, calcium carbonate, chemical raw materials, food, and other items, and can also be used to store water or wastewater in special environments. However, fiberglass silos have their shortcomings. For example, they may lack rigidity and be prone to deformation; they have poor long-term temperature resistance and cannot be used for prolonged periods in high-temperature environments, which limits their application in certain fields; exposure to ultraviolet light, wind, sand, rain, snow, chemical media, mechanical stress, etc.; can lead to a decline in performance and aging; initial costs are higher compared to traditional materials; and specialized knowledge and technical expertise are required for construction and maintenance.
Considerations for Silo Material Selection
When choosing the material for silos, buyers need to consider the following aspects:
1. Environmental Adaptability: Selecting suitable materials based on the climate and environmental characteristics of the storage area to ensure that the silo can maintain a stable storage environment under different climate conditions.
2. Moisture and Pest Resistance: The silo material should have good moisture and pest resistance to protect the quality and safety of the stored materials effectively.
3. Structural Stability: The structural stability of the silo is crucial for the long-term storage and protection of materials. Materials with sufficient strength and durability should be chosen.
4. Construction and Maintenance Costs: Considering the construction and maintenance costs of the silo, choose materials that are easy to maintain and clean to prolong the silo's lifespan.
5. Degree of Mechanization and Standardization: Silos need to have technological and standardized management systems that can monitor the storage status of materials in real-time.
In summary, the choice of material for silos is one of the key factors in ensuring the safety of the materials stored inside. Different materials have their own characteristics and applicable scenarios. Buyers should comprehensively consider their actual needs and conditions to ensure that the silo can effectively protect and store materials, meeting the safety and supply requirements of the materials.
Previous:How To Choose A Metal Silo?
Get In Touch With