Application Research and Design Optimization of Large Fly Ash Silo System
Fly ash is a fine ash collected from the flue gas after combustion of coal, and fly ash is the main solid waste discharged from coal-fired power plants. The main components of fly ash are SiO2, Al2O3, FeO, Fe2O3, CaO, TiO2, etc. With the development of electric power industry, the amount of fly ash emitted from coal-fired power plants has increased year by year, which has become one of the industrial waste residues with large displacement in China. In 2015 China's total emissions will reach 0.58 billion tons, forming a heavy burden on the environment.
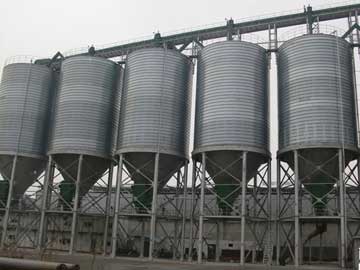
If a large amount of fly ash is not treated, it will cause the dust and air pollution; if it were to discharge into water system, it would cause the blockage of the river, of which the toxic chemicals may do harm to humans and creatures. So people have continuously been making the deep research on the complex utilization of fly ash and found out many applications, for example, it can be used as a concrete admixture. However, the premise of the application is efficient and environmentally friendly storage. In the world steel silo is the best choice till now. We also manufacture fly ash storage silo onsite.
Classification
The large fly ash silo usually refers to the reserves of 10 thousand tons or more or the diameter of the quasi 18m or more, the steel silo system generally consists of four parts: the base, the silo, the discharging system and the automatic control system. Currently there are several classification:
- According to wall structure of steel silo: spiral undercut type, welding type and assembly type;
- According to arrangement of steel silo: half elevated type, elevated type and ground type;
- According to the quantity of discharging point of steel silo: single-point discharging type and multi-point discharging type;
- According to conveying mode of discharging: pneumatic conveying type, mechanical conveying type, combination type of mechanical and pneumatic conveying;
- According to fluidization mode of fly ash: fluidized bar type and air box type;
- According to loading way: elevated direct loading type and bulk warehouse loading type and so on.
Spiral Fly Ash Silo
Here we have to mention the spiral fly ash silo.
The spiral steel silo adopts the technology of site construction. Silo roof is installed on the ground and then lifted up to the top of silo. In construction process, forming equipment, bending line can work at the speed of 5m/min, which does not need the help from the scaffolding and other auxiliary facilities. So construction duration is rather short. The whole silo wall is made with high-quality galvanized thin steel plate, so the silo wall will not generally paint, which greatly reduces the cost of construction and maintenance. At present in China, the effective storage capacity of spiral steel silo is about 10,000m3, whose maximum size is D22m×H27m.
In conclusion, if we choose spiral steel silo to store fly ash, fly ash silo will have many outstanding features or advantages as below:
- Low cost: compared with the other structural silos, it can save the construction cost of about 30% ~ 50%.
- Short Installation: compared with the other structural silos, it can save much time. Take 1000 ton cement silo for example, it will take 7-10 working days to install one spiral steel silo, while cement silo will take at least 20 days to install.
- Good water-proof and anti-corrosive protection: it is made of galvanized steel plate which is not only waterproof, but also anti-corrosive.
- Good leak-proof and damp-proof protection: using the advanced technique of sealing, it has good sealing performance.
The fluidization mode of large fly ash silo
Air box type
Generally the plate air box used is 3mm thick, whose breathable layer is now made of polyester canvas or silicon carbide. Technical performance is as shown in table 1~2.
Type | Layer Number | Thickness(mm) | Weight (kg/m3) | Tensile Strength(MPa) | Temperature Resistance (℃) | Ventilation Volume(m3/m2`min) | Elongation(%) | Allow Gas Pressure (MPa) |
---|---|---|---|---|---|---|---|---|
PET-6 | 5 | 6 | 4.5 | >50 | 150 | ≥3 | ≤7 | <0.4 |
Type | Density(/g/cm3) | Compressive Strength (MPa) | Flexural Strength (MPa) | Permeability (%) | Temperature Resistance (℃) |
---|---|---|---|---|---|
QHP | 1.7-1.8 | 20 | 12 | 47.5-48.5 | ≤200 |
Fluidized bar
For a common fluidized bar, its inner bar is made of a circular DN40 steel tube with air holes after the precise calculation and strict selection. The inner bar is wrapped in a layer of good quality of filter cloth which has features of wear resistance and corrosion resistance. Stainless bellows steel tube with 50mm in diameter can withstand the material pressure and the various impacts from the inner silo. The lowest allowance temperature is minus 30℃, the highest temperature 150℃ under constant temperature, air permeability resistance≥17kPa. The fluidized bar may be installed on wherever it needs as required, which distance between two is about 1000mm. General fluidization pressure is 98.0kPa, air is generated by Roots blower; dredging pressure is 0.2-0.4MPa as the gas source using compressed air.
Gasification of fluidized bar belongs to linear gasification mode, which has features of high pressure and low gas consumption, and can disturb upper storage material more favorably and make its foundation instability collapse and flow. So the mode is suitable for ground type of steel silo. The mode is simple for installation, and can bear strong pressure and high abrasion, thereby reducing the frequency of replacement and operating costs.
Conveying mode of large fly ash silo
Horizontal conveying part
Pneumatic conveying type
For ground steel silo, the part from unloading hole at silo bottom to horizontal part at out-lateral silo, usually can be used in the feeding pipe. The feeding pipe is provided with a fluidized bar with compressed air. Compressed air goes into the conveying pipe through the air permeable layer. The storage material in the feeding tube has been in fluidization. Power of material conveying comes from: a. the material flow pressure produced by fluidized bar in the unloading pressure zone; b. main airflow from the feeding pipe and the auxiliary blowing airflow; c. negative pressure induced draft of dust collector at the feeding hole of the elevated machine.
Mechanical conveying type
The part from unloading hole at silo bottom to horizontal part at out-lateral silo, also can be used in air slide or conveying machine of buried scraper. Air slide conveying can save much energy, but shall be arranged in a certain slope (6 to 10 degrees). Conveying corridor has huge height difference, so that will increase the construction cost. Conveying machine of buried scraper can be arranged horizontally or slightly upward, which saves the construction cost, but increases the power consumption more, adds maintenance costs.
Elevated conveying part
Mechanical elevation type
The steel core belt bucket elevator or plate chain bucket elevator is usually used now. Steel core belt bucket machine adopts high strength steel wire rope of tear-proof rubber belt, which overcomes the dynamic loading caused by the plate chain meshes with the chain wheel when driving, but lifts more portably, operates more stably, lowers noise and maintenance cost.
Pneumatic elevation type
For pneumatic elevation type, the air consumption is large, the energy consumption is high, and the wear is faster.
The promotion of large fly ash silo system will facilitate the comprehensive utilization of fly ash in fire power plant to reach 100%, saving the total investment of the project, which has positive significance for promoting the development of low carbon economy.