An Introduction to The Hopper Silo
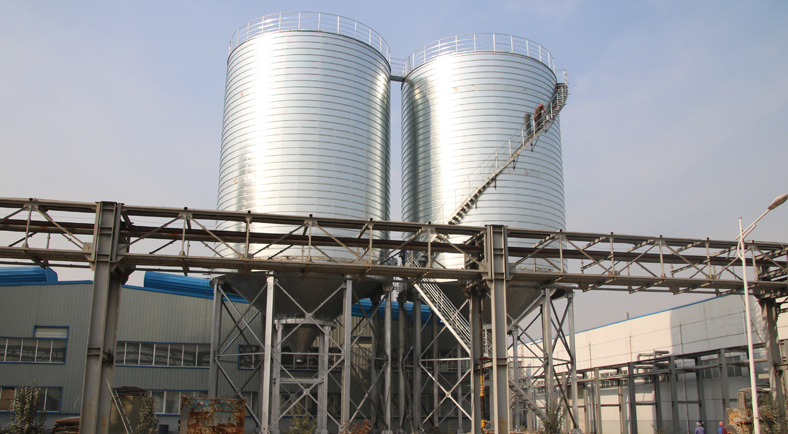
Steel silos come in two types of bottoms: flat and cone-shaped. Each has its own advantages and unique architectural features. The cone bottom silo is also known as the hopper bottom silo, which is built with a steel frame structure. Compared with the flat bottom silo, the hopper silo is designed to be conical and has a variety of uses.
Basic Structure
Silo BodyThe silo body is the core part of the hopper silo, and its structural forms are mainly cylindrical, conical, rectangular, and so on. Among them, the cylindrical silo has the advantages of simple structure, convenient manufacture, and wide application.
Design details:
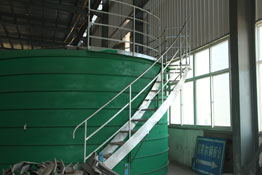
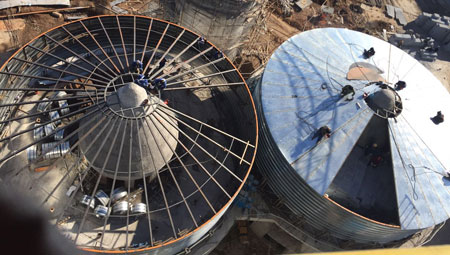
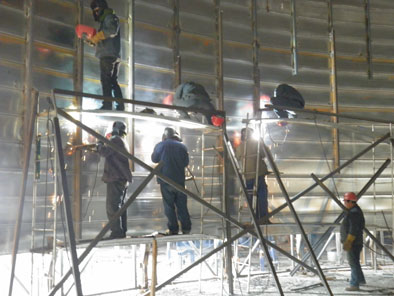
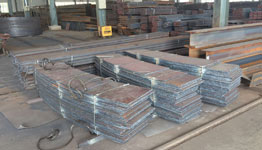
The Angle of the silo roof is generally designed to be 25 to 30 degrees, and it is firmly fixed on the silo by welding. The interior is reinforced with multiple suction guns so that the silo can withstand the harshest environments. The warehouse door adopts internal and external double doors with good sealing, safety, and corrosion resistance.
A ladder is built outside the silo for workers to check the condition of the silo, and the ladder can lead to the top of the silo. Handrail provides convenience for the operation of workers and ensures the safety of workers. The rest platform is designed for workers who check the condition of silos, and for workers who work for a long time, there can be a relatively safe place to rest.
The Lipp steel silo double seam technology used by AGICO is the patented technology of Xavef Lipp, a German technical engineer. It adopts a metal plastic work hardening principle and a thin shell structure. The use of special technology and equipment, coated 2 ~ 4 mm thick galvanized steel plate (or stainless steel). According to the "spiral, double seam, cleaning" process it create a volume of 100 to 5000 cubic meters of Lip steel silo. The edge of the steel belt is folded twice to make the two pieces of material bite tightly and the sealing effect is good. In addition, the zinc content of the galvanized coil we use is 275g/m2, which is higher than the national standard, which also better guarantees the corrosion resistance and longer service life of the silo. The silo body is reinforced with steel bars, and the reinforcement welds on the plates are fixed with double-welded plates, which enhances the stability of the silo.
Feeding and Discharging Device
It mainly includes parts such as inlet and outlet, inlet and outlet pipe, inlet and outlet valve, etc. The feed port is located in the upper part of the silo body, the discharge port is located in the lower part of the silo body, the feed pipe and the discharge pipe are connected to the silo body, and they are used for conveying materials. Feed valves and discharge valves are used to control the flow rate of materials and prevent material clogging.
Supporting Device
It mainly includes columns, beams, longitudinal beams, and other components. The column is used to support the weight of the entire hopper silo to ensure its stability; The beam connects the column and the longitudinal beam to play a strengthening role; Longitudinal beams are used to support the silo body and the inlet and outlet devices.
Structural Characteristics
Ease of operation is the most significant advantage of the hopper silo. The hopper bottom silo is easier to discharge, and the material stored in the silo can be discharged by its gravity, without relying on other auxiliary equipment. The cone base design also eliminates gaps, reduces the amount of work required to maintain the silo, and also reduces the damage of accumulated material to the silo. The bottom of the hopper adopts an all-metal structure. The construction of this step can be completed in the factory in advance, which will effectively reduce the construction amount and shorten the construction period. The relocation of the silo is relatively easy after completion.
In addition, the advantages of hopper silos are also reflected in the following aspects:
Large storage capacity: The design of hopper shaped steel silo makes it have a large storage capacity, which can meet the needs of large-scale production and use.
Small footprint: Compared with traditional concrete silos, the design of hopper-shaped steel silos is more compact, effectively saving the floor space.
High safety: The structure design of the hopper-shaped steel silo is reasonable, which can effectively prevent the collapse and overflow of materials and ensure production safety.
Easy maintenance: The inner wall of the hop-type steel silo is smooth and smooth, which is easy to load and unload materials and clean up, but also conducive to later maintenance and maintenance.
Application
Hopper silos are designed to prevent moisture from reaching the materials stored inside. Because of this characteristic, hopper silos are widely used for grain storage. Similar to flat silos, the bottom bin of the hopper can also be designed and installed with insulation devices to meet the special needs of heat storage. In addition, it can be used for temporary storage as part of other buffer silos in grain drying equipment and silo equipment.
From a practical point of view, we recommend choosing the hopper bottom bin because it has the advantages of no inventory, no need to configure customs clearance equipment, etc. If it is a larger size silo, the cone bottom design will have certain limitations in cost. Still, for silos with a diameter of no more than 10m and a capacity of no more than 1500t, the hopper bottom silo is more cost-effective.
If you need it, please feel free to contact us, AGICO can customize different sizes of hopper silos for customers.
Get In Touch With