The Manufacturing and Installation Process of Steel Silos
With the wide application of steel silos in the wharf, port, grain depot, as well as oil, flour, food, alcohol, feed, and other industries, it has increasingly become the main equipment for modern bulk materials storage. The advantages of steel silo are obvious, such as high strength, light weight, long life, low cost, low requirement for foundation, and a high degree of standardization. It can be prefabricated in the factory, features simple assembly, strong mobility, and easy to leave space for expansion. At present, various types of steel silos are sold in the market, such as spiral steel silos, bolted steel silos, and welded steel silos. They have different characteristics and manufacturing and installation process. Next, we will introduce these silos in detail.Steel Silo | Features |
Spiral steel silo | Low cost, lightweight, and good sealing performance |
Bolted steel silo | Short constructing period and detachable |
Welded steel silo | Good corrosion resistance and long service life |
Spiral Steel Silo
Due to solving the problems of safety, service life, materials, and supporting facilities, the steel silo has been developed rapidly. In 1968, the German Lipp invented the spiral steel silo (also known as Lipp silo or spiral silo) that was built with SM special equipment. In 1969, the first spiral steel silo was built in Germany. At present, the diameter of spiral steel silos can be selected from 3 to 25 m, and the maximum height-diameter ratio (height of silo body divided by diameter) can reach 5.75.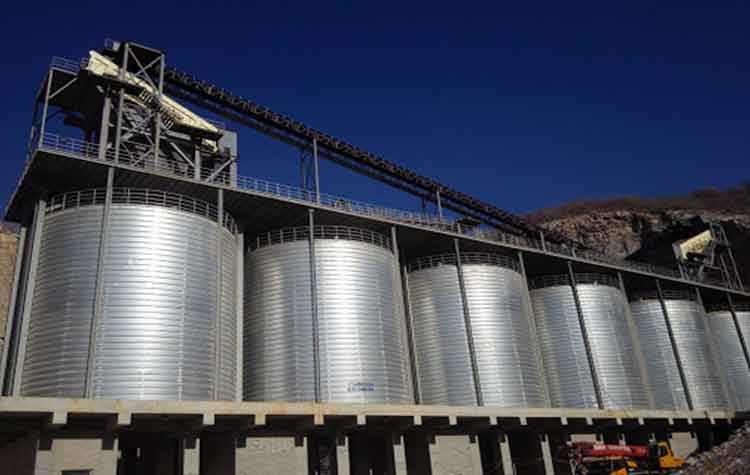
Manufacturing and installation process: first of all, we should transport all the silo manufacturing equipment to the construction site, and then complete the continuous bending and biting of the galvanized coil plate according to the procedures of uncoiling, forming, undercutting, pushing, and rising to realize the construction of silo sidewall.
During the construction, 495 mm wide coil plates will be fed by the unwinding machine into the forming machine to form the desired shape, and then be bent and bitten through the undercutting machine to form a 30-40mm wide continuous helical convex rib outside the sidewall of the steel silo. In this way, the rolled coil plate spirally rises to form the sidewall of the silo driven by several running racks and riding wheels. In the later forming process of the sidewall, we will install vertical stiffeners close to the inside of the sidewall to play a supporting role. When the sidewall height reaches about 1m, we should install the silo roof, and when the sidewall reaches the preset height, the whole steel silo will be fixed on the foundation.
Advantages: lightweight, high strength, long service life, short construction period, low cost, good airtightness, a high degree of mechanization, wide application, and wide applicability.
Disadvantages: the storage capacity is limited (the diameter is no more than 25 m, and the storage capacity is no more than 6500 t).
Bolted Steel Silo
The wall of the bolted steel silo is mainly composed of profiled steel sheets and Z type steel studs. Small silos and short silos may have no stud or only single stud, while large silos and high silos must have double studs. The profiled steel sheet is made of rolled coil plates in one step by pressure-rolling process. After the ripple is formed, the silo wall will be finally prefabricated through the punching process, arc bending process, and galvanizing process, and then be packed and transported to the warehouse or site for installation. The maximum diameter of bolted steel silos is up to 32m, and the largest capacity can reach 17000 t.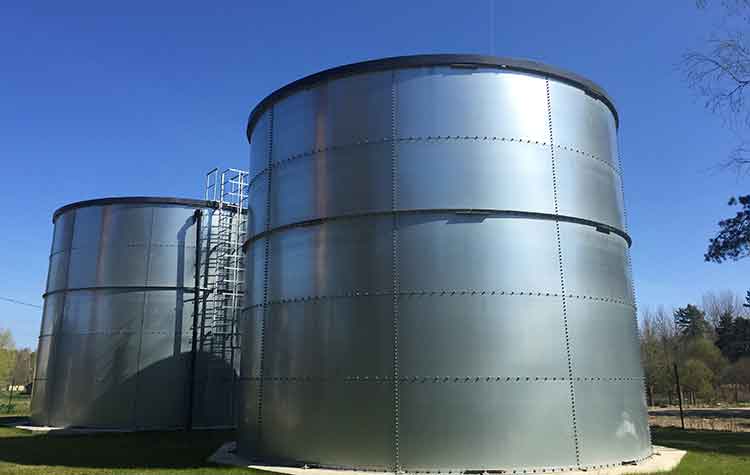
Manufacturing and installation process: first of all, we need to produce all the components (roof, sidewall, etc.) needed for steel silo construction and transport them to the installation site. After the site preparation is completed, we should locate the position, install and fix the lifting appliance according to the steel silo diameter. During the silo body construction process, the molded steel plates and stiffeners are connected in sequence by high-strength bolts. When installing the second ring, we need to start installing the silo roof and then continue to work on the silo body. After the silo wall reaches the set height, connect the whole silo body with the embedded parts.
Advantages: lightweight, simple assembly, detachable, low cost, low requirement for foundation, and a high degree of standardization.
Disadvantages: the sealing performance is slightly inferior to that of spiral steel silo, and the maintenance cost is high.
Welded Steel Silo
With the development of welding technology, people began to build steel silos with 4-12mm welded steel plates. The airtightness of welded steel silos is good. Because of the thick silo wall, its strength is large and can be built higher. Besides, the service life of a welded steel silo is relatively long, as long as the maintenance is proper, it can be used for 50-80 years. In coastal ports, due to the corrosion of steel plate by salt in the air, as well as the large throughput and large storage capacity of the port, thick steel plate welded steel silo is the most suitable choice.Advantages: good air tightness, thick steel silo wall, high strength, high height, good corrosion resistance, and long service life.
Disadvantages: high labor and raw material costs, long construction period, and high construction difficulty.
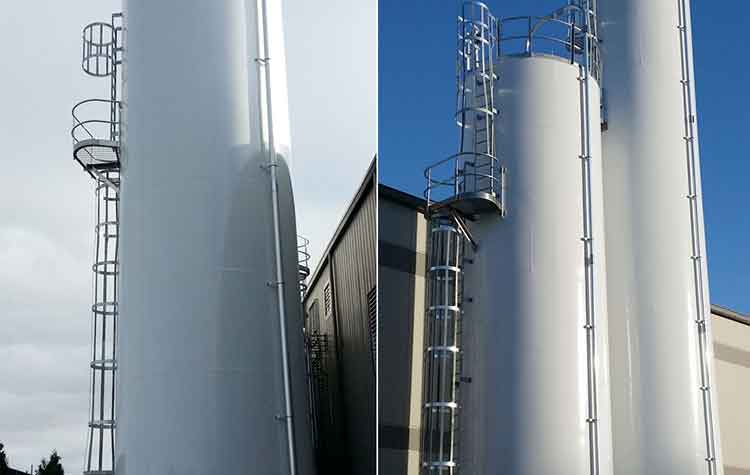
Get In Touch With