Steel Silo Corrosion Types And How to Prevent Them
Steel silos are dry bulk storage containers. Cment silos, fly ash silos, grain silos, and coal storage silos are all steel silos.The construction material of steel silos is ordinary steel. Steel is a metal product, and most metal products will inevitably face corrosion problems. The steel silo will certainly be subject to corrosion from various aspects during use, and the corrosion will greatly reduce the service life of the steel silo. Therefore, effective measures must be taken to prevent the occurrence and development of the corrosion phenomenon. So how can we prevent this from happening? This article will do analysis and put forward some necessary measures to be taken against corrosion of the steel silo.
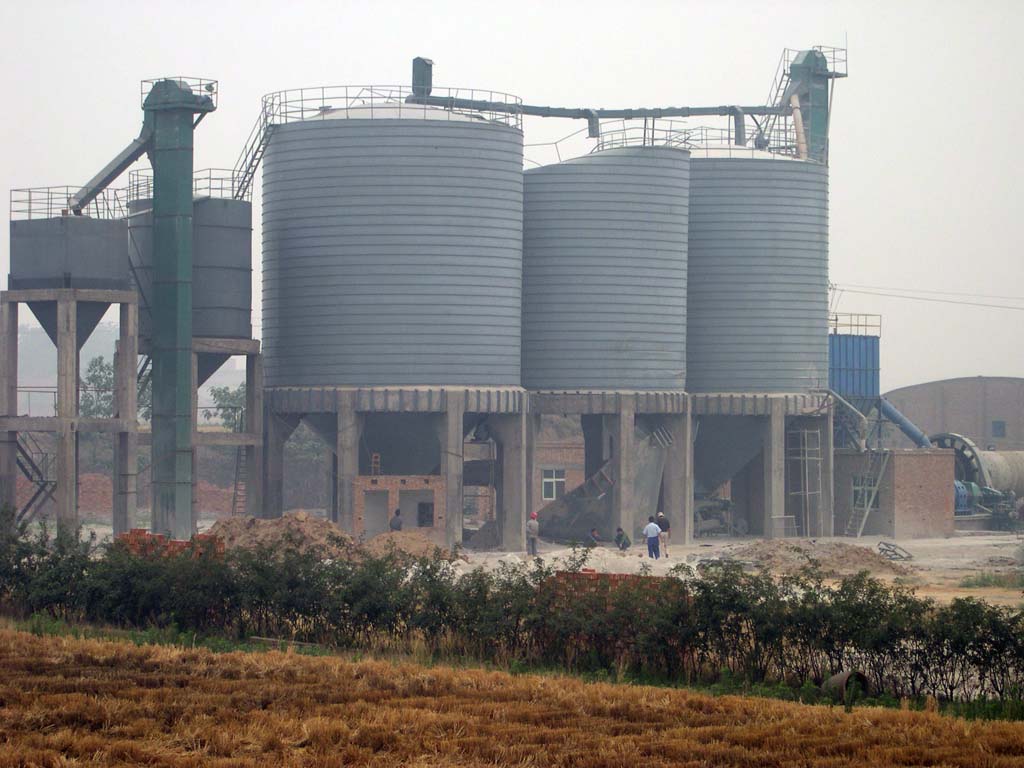
What is the corrosion of the steel silo?
Corrosion of the steel silo can be divided into atmospheric corrosion and chemical corrosion according to the causes.
1.Atmospheric Corrosion
Atmospheric corrosion is one of the earliest causes of metal corrosion discovered by humans. Atmospheric corrosion occurs in metals, either indoors or outdoors. The steel silo is placed and used in open air in the atmosphere. Compared to other types of environmental corrosion, atmospheric corrosion is a more common phenomenon.
In different parts of the earth, in different seasons and at different times, people always face different atmospheric environments. Steel silos are exposed to different atmospheric conditions and are subject to varying degrees of atmospheric corrosion. For example, compared to temperate regions, steel silos are more vulnerable to corrosion from atmosphere in rainy regions, hot and arid regions, cold and snowy regions, and areas with high humidity and salinity.
Furthermore, due to the rapid economic development of modern society, the atmospheric environment has been artificially damaged. At present, the composition of the atmosphere is also accompanied by many toxins, and the corrosion of steel structures is also serious. In particular, the strong acid and alkali gases directly make the steel structure buildings completely different.
The steel used in the construction of steel silos is a very good building material, and its requirements for the atmosphere are relatively high. Given that the current environment is highly corrosive to steel silos, it is very important to take measures against atmospheric corrosion. In order to increase the service life of the steel silo, the customer and the builder should pay attention to selecting the appropriate thickness of the galvanized steel plate as the basic structural material. If you want to obtain a thick galvanized layer, the surface treatment before galvanizing should use sandblasting instead of pickling.
The overall design of the steel silo should be adapted to local conditions.
2.Chemical Corrosion

What are the specific measures for preventing corrosion in steel silos?
The basic layer need to be completely cleaned up, and special equipment is used for grinding and rust removal or sandblasting and rust removal. There must be no rust spots on the base after derusting, and oil, grease, dust, iron sand and metal oxides should be cleaned up. After derusting, the primer must be applied within six hours for corrosion protection. Before the spraying process, if it rains or other conditions that cause the surface of the substrate steel to be wet, it should be blown with dry compressed air after the environment reaches the construction conditions. Dry surface moisture after rust removal; derusting of the steel surface to achieve rust level Sa2.5, the surface with a brush and other tools to clean the next process, after derusting qualified steel surface appears metallic luster, per square meter Metal surface rust and paint shall not be greater than 5%, such as rust before the priming, re-grinding rust or sandblasting rust, can not reduce the abrasive requirements, so as not to reduce the roughness.
The steel silo needs to use high-pressure cleaning equipment to clean the surface of the basic layer, and thoroughly clean the basic layer crevices, concave-convex parts and concealed corners. The base surface must be firm and flat, and the uneven or cracked parts must be reinforced before the construction; the base surface must be removed completely and clean, with no dirt, dust, debris, water, oil, or loose materials, etc. And always pay attention to keep the base clean and hygienic.
Get In Touch With